When two stainless steel parts are in direct contact with one another, the constant friction can result in galling of the metal. Just ask Cutting & Wear Limited (C&W). C&W are an international supplier of downhole tool technology to equipment manufacturers worldwide. C&W contacted SIFCO Applied Surface Concepts because they needed to selectively plate a thin layer of copper for anti-galling purposes onto the threads of newly manufactured stainless-steel components while meeting their customer specifications.
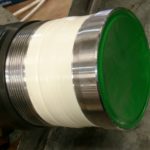
C&W manufacture Flow Exit Cylinders for the oil & gas industry. The cylinders are made out of UNS S17400 H900. UNS S17400 H900 is a chromium-copper precipitation hardening stainless steel that is used for applications requiring high strength and corrosion resistance. Due to the base metal material, the threaded connection of the cylinder is threatened by galling, corrosion, and leakage. Adding to the difficulty, often the ends of the cylinders are treated with a delicate “Zintec” coating, which can be easily damaged.
C&W had investigated multiple options to provide the lubricity and anti-galling properties they required. Unfortunately, both options posed too big of a risk to the part and to the existing Zintec coating. Barrel plating – a process in which components are placed in an electrolyte solution in a barrel, then rotated or tumbled to provide an even coat – was discarded because the fragility of the components. While tank planting was rejected because the cylinder components would need to be heavily masked to protect Zintec coated ends. Also, tank plating was not financially viable due to the small quantity needing plating.
The answer came in the form of selective plating. The SIFCO Process® of selective plating, is a portable electroplating method used to enhance, repair, and refurbish localized areas on manufactured components without the use of an immersion tank. As only a small deposit of copper was needed to provide the lubricity and anti-galling required, and with the volume of components being low, selective plating was chosen as the ideal procedure. By using isolated masking techniques and a power pack, technicians were able to plate within drawing tolerances without the need for post machining.
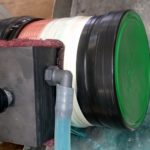
Prior to the application of copper, the parts were carefully masked to protect the Zintec coating. Selective plating requires movement of the anode, the part, or both. For this application, the cylinders were placed in a turning head, or lathe, while the operator held the anode stationary, ensuring good flow to the anode for quality deposits on the deep threads. The initial pre-plate procedures were: Electroclean, Activator No. 4, Activator No. 1, and Nickel Special for bonding. Copper was then deposited onto the deep threads, allowing for the right amount of lubricity and anti-galling on the mating parts.
By using selective plating C&W was able to plate a limited quantity of components in less than half the time it would have taken for tank plating, and at less cost. And SIFCO ASC now plates these cylinders on a regular basis. According to James Kilner, Production Data Controller at C&W, “We use SIFCO ASC because their work is always of high quality, they always turn our parts around in good time, and they have excellent customer services. We wouldn’t use anyone else for our copper coating.”
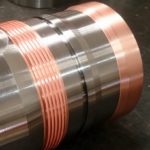
For more information on our anti-galling coatings, or plating of threads and grooves, visit www.sifcoasc.com/oil-gas